Rubbish removal and demolition are evolving fast in today’s urban world. New challenges push innovation forward. Old methods are no longer enough. Cleaner and smarter ways are in demand.
Technology has changed how debris is tracked and managed. Drones now scan demolition zones before work starts. AI programs help sort materials more efficiently. This reduces waste and improves speed. Visit paulsrubbishanddemo.com/ to learn more.
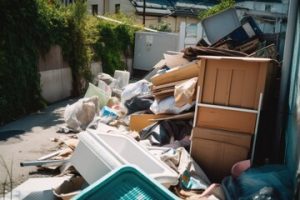
Sustainability is no longer optional in debris handling. Demolition crews now separate recyclable parts on site. Salvaged wood and metal find new purposes. Less ends up in landfills each year.
Invisible waste is now getting attention. Dust and micro-particles were once ignored. Now, portable air filters are installed during takedowns. These limit health risks for workers and neighbors.
Noise pollution is another hidden issue. Smart sound barriers are used during teardown. Vibrations are dampened with new equipment. Neighborhoods experience fewer disruptions.
Underground scanning has become essential. Before demolition, teams map buried wires and pipes. This prevents accidents and expensive damage. It also shortens overall timelines.
Digital twins now model entire buildings before removal. These 3D models simulate the structure’s collapse. Engineers predict the safest path for each fall. Safety and planning improve dramatically.
Robotic demolition is gaining popularity in tight spaces. Small machines break walls with great precision. They reduce human risk in unstable zones. Efficiency also increases without sacrificing control.
Smart bins assist in post-demolition cleanup. They use sensors to sort rubbish automatically. Recyclables go into one area, the rest in another. Workers handle less mess and fewer errors occur.
Eco-friendly materials are now key even in disposal. Biodegradable containers carry smaller debris loads. Trucks use electric power instead of diesel. The environmental impact is shrinking.
Some demolition projects are now “soft tear-downs.” Instead of destroying everything, they disassemble parts. This protects heritage elements and reduces waste. Valuable pieces can be reused in future builds.
Permits and paperwork have gone digital too. QR codes track every stage of demolition. Waste is logged in real-time. Authorities can check compliance with one scan.
Rubbish removal also faces a shift in priorities. It’s not just about hauling junk anymore. It’s about resource recovery and environmental responsibility. The mindset is changing across industries.
Smart apps let residents schedule rubbish pickups online. AI predicts the best time for collection. Routes are optimized to save fuel. The process feels seamless for the user.
Reused concrete is getting attention as a base layer. Crushed chunks serve as foundations in new builds. This reduces the need for fresh raw materials. It’s a smart form of circular economy.
Asbestos disposal follows stricter new protocols. Special bags seal in harmful particles tightly. Trucks are tracked through GPS from site to site. Health and safety are top priorities.
Illegal dumping is being curbed with motion sensors. Remote areas now have smart cameras installed. They detect unauthorized rubbish drops. This discourages harmful environmental behavior.
Demolition timelines are getting tighter with better forecasting. Teams use data to plan around weather. Delays are minimized, and output increases. This boosts productivity without compromising safety.
Emergency demolitions now use modular response kits. These are ready to deploy in disaster zones. They include portable machines and rapid setup gear. Lives are protected and time is saved.
Schools and hospitals require more care during nearby demolition. Barriers and shields block falling dust. Specialized teams monitor air quality nonstop. Sensitive zones stay safe throughout the process.
Concrete slurry is being managed more responsibly. Special pads soak up excess liquids fast. They’re then filtered for reuse or safe disposal. Water pollution is kept in check.
Green spaces near demolition zones get protective netting. This prevents debris from harming plants. Landscape preservation is now part of standard procedure. Urban beauty is maintained.
Training now includes virtual reality simulations. Workers practice in lifelike environments. This builds muscle memory before stepping on-site. Errors drop significantly through immersive learning.
Salvage yards have modernized operations too. Robots scan materials and catalog them digitally. Inventory is updated in real-time. Reselling and reuse become easier and faster.
Floating demolition sites are appearing in coastal zones. These platforms dismantle sea structures without harming marine life. Waste is transported via sealed containers. This protects delicate ecosystems.
Mobile shredders allow onsite processing of certain rubbish. Materials are ground down for easier transport. This reduces fuel use and space needs. Landfill trips are minimized.
Mental health support for demolition workers is growing. High-stress jobs are finally getting attention. Counselors are available for trauma support. This improves job retention and well-being.
Noise mapping software helps plan quieter takedowns. Teams identify peak noise zones beforehand. Equipment is adjusted to reduce disturbance. Residents report fewer complaints as a result.
Biometric scanners now control site access. Only authorized staff can enter demolition areas. This prevents theft and ensures safety. Accountability also improves with every scan.
Wearable tech monitors worker stress in real-time. If someone overheats or becomes too stressed, alerts go out. Supervisors act fast to prevent injury. Technology adds a new safety layer.
Flood-prone zones use floating barriers during teardown. These keep runoff from polluting waterways. Rubbish is then collected safely and cleanly. Natural resources stay unharmed.
Old appliances are dismantled for their rare earth elements. These metals are reused in high-tech devices. Rubbish becomes valuable again. It’s a win for both business and environment.
Smart helmets now include AR overlays. Workers see structural data in their line of sight. This guides safer cuts and removals. Efficiency and safety both improve.
Rubbish audits are becoming routine before any teardown. Teams assess what will be removed, reused, or recycled. Reports guide the entire process. There’s less guesswork and more intention.
Insurance policies are adapting to smart demolition risks. Coverage includes AI-based errors and robotic mishaps. Claims are processed digitally. The financial side keeps up with the tech.
Public awareness campaigns now highlight clean demo practices. Communities learn how their waste is handled. This builds trust and cooperation. People begin to care more about the process.
Some firms are turning demolition into education. Students watch live takedowns virtually. They learn about engineering, ecology, and safety. It’s a unique and valuable real-world lesson.
Cloud platforms store project data across demolition stages. Everyone sees updates in real-time. This improves coordination among teams. Mistakes are reduced and progress stays smooth.
Construction firms partner with demolition experts early on. This helps prepare for future teardowns in the design phase. Materials are chosen with reuse in mind. It’s forward-thinking and resource-wise.
Fire-damaged buildings require special removal methods. Heat-weakened structures collapse differently. AI models predict safe strategies. Risk is managed with scientific precision.
Hazardous materials like lead paint are pre-flagged. Thermal scanners detect them quickly. Teams then isolate these zones. Cleanups are safer and more efficient.
Demolition near historic sites uses vibration control mats. These shield nearby structures from tremors. Sensitive architecture is preserved. The past and present coexist more peacefully.
Eco-certifications are now offered for clean demolition. Firms compete for recognition based on practices. Clients prefer certified teams. It becomes a mark of excellence and trust.
Workers log incidents through voice command apps. No need to stop and write. The data is instantly uploaded. Field communication becomes easier and safer.
Drone footage is used not only for planning but also for transparency. Public can view takedown progress. This builds trust in regulated processes. Openness reduces resistance and fear.
Smart contracts automate payment after rubbish is cleared. Sensors confirm site cleanliness. Payment is released instantly. There’s no delay or dispute.
Temporary recycling plants operate near major demo sites. Debris doesn’t have to travel far. It’s processed immediately for reuse. Local supply chains benefit.
In high-density zones, vertical rubbish lifts are used. Debris moves upward instead of across crowded streets. This reduces traffic and chaos. Cleanup is smoother and more contained.
Worker uniforms now include air quality sensors. Bad readings trigger automatic alerts. This prompts immediate action on site. Lives are saved through wearable awareness.
Urban farming projects use rubble as base layers. Crushed concrete helps with drainage. It supports rooftop gardens and green zones. Waste finds surprising second lives.
Every year brings new ideas in rubbish removal and demolition. What was once waste is now a resource. Smart systems and green goals lead the way. The future of urban cleanup is bright and responsible.